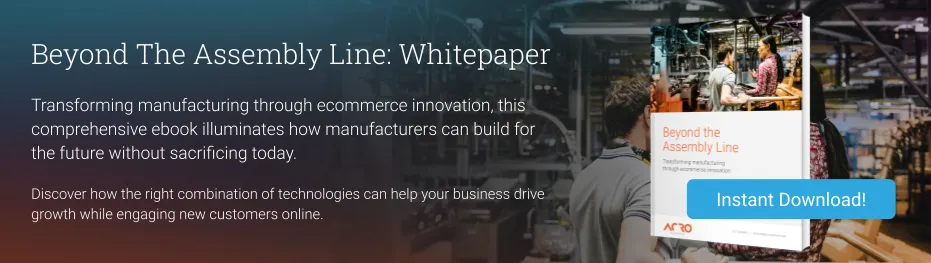
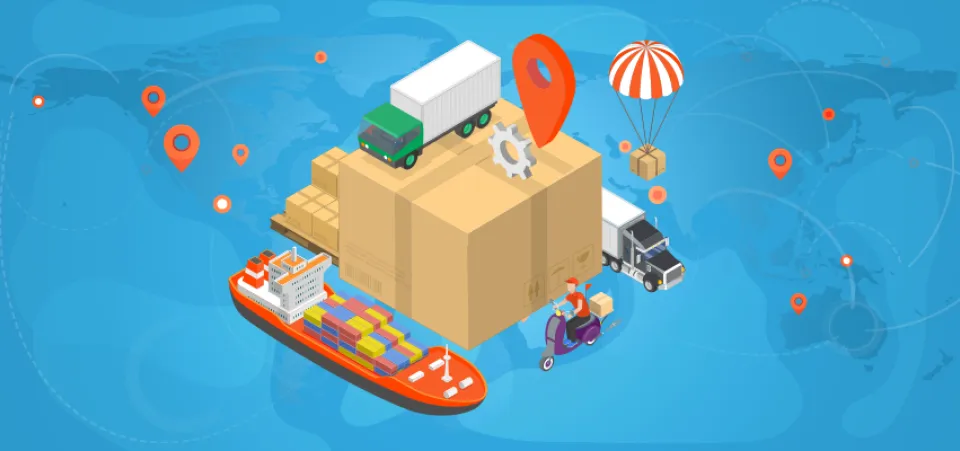
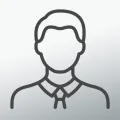
November 23, 2022
How manufacturers can enhance supply chain resilience
Manufacturers have always understood that supply chain disruption is a risk, but nothing prepared the industry for the scale of disruption triggered by the COVID-19 pandemic. This article outlines several ways manufacturers can prepare for future disruptions.
Seven supply chain strategies for manufacturers to improve resiliency
Many businesses were caught flat-footed with shortages and transport problems not seen since WWII. They had to create a patchwork of contingency measures to maintain operations quickly. Emergency shipments, costly cargo movement and congested ports characterized the pandemic’s peak.
Disruption has costly consequences and significantly impairs earnings. As the effects of COVID-19 petered out, conversations in manufacturing boardrooms centred around recalibrating supply chains to boost resilience.
So how do you do this? Let’s explore some practical supply chain strategies for manufacturers.
Strategies for improving supply chain efficiency
Proactive supplier management
Supply chain resilience must start with a deep and accurate understanding of your suppliers. Assess your suppliers and rank them by their criticality to your business. Get a detailed view of multiple tiers of your suppliers’ suppliers to perform an exhaustive assessment of the upstream risks. Use KPIs to gauge suppliers' ongoing reliability, credit risks, and location concentration.
Where possible, have suppliers share important data regularly. This depth of insight helps you pick up potential weak spots well before a disruption occurs. You have ample time to establish safeguards that protect your factories’ continued operations.
Create capacity and inventory buffers
Creating capacity buffers is perhaps the simplest and most widely used approach to enhancing resilience fast.
Manufacturing managers already understand and encounter buffers when raising capacity in anticipation of new growth or product launches. When done for purposes of supply chain resilience, though, the goal is more long-term.
Resilience buffers could take multiple forms:
- underutilized manufacturing facilities
- surplus inventory over safety stock levels
- contracting specific suppliers for unexpected disruption
A key drawback of this technique is that buffers are costly. Supply chain managers will find it difficult to justify this expense to senior management.
Diversification of supplier location
Over the last 40-odd years, global manufacturing has shifted East. Many manufacturers’ supply chains heavily depend on China, East, South, and Southeast Asia.
If you are in a similar predicament, consider enhancing your resilience by diversifying source markets away from any one country or region. For example, consider sourcing vendors in Mexico if most of your suppliers are in China. That will not always be possible, but even shifting to a different country in Asia would lift your resilience a notch.
Like creating buffers, spreading suppliers across regions may increase costs due to a loss of economies of scale and the freight rates pricing advantages countries like China have over much of the world.
Multisourcing
Sourcing from one country is risky. Sourcing from one company is worse. It creates a single failure point that could grind your production to a complete halt. Multisourcing helps you mitigate such dependency.
To create multi-sourcing that works, start by categorizing your suppliers by importance based on the dollar value of the business you have with them and its impact on your operations if events unexpectedly cut off that supply.
Ordinarily, you achieve multisourcing by awarding contracts to multiple suppliers. However, you can multisource by contracting one supplier with multiple production/processing locations. This second option should be a last resort if working with multiple suppliers proves unfeasible.
Nearshoring
Manufacturers adopted offshoring to maximize profit and unlock long-term value for shareholders. But as offshoring experienced various shocks, business leaders soon realized the growth advantages were not without serious drawbacks. A key concern was the long, costly, and often complex route supplies had to navigate before getting to the factory floor.
An incident along this path could impair the manufacturer's operations, even if it had nothing to do with the supplier. Think about the six-day obstruction of the Suez Canal by the Ever Given that upended supply chains, delayed tens of billions of dollars in trade, and caused losses exceeding a billion dollars.
Manufacturers are switching to nearshoring to mitigate these risks by working with suppliers in or near their home countries and cities.
Strategic partnerships with suppliers and 3PLs
No business operates in a vacuum. Dependence on third parties is the very reason for supply chains. But supplier contracts alone are insufficient to protect your factories from the effects of supply chain disruption. Your suppliers likely have ’regular’ contracts with multiple manufacturers besides you.
Instead, seek to establish partnerships with key suppliers. And if you do not have factories in multiple locations that could boost your operational resilience, establish collaborative partnerships with logistics firms (such as 3PLs) as well. Partnering with 3PLs ensures your supplies and products are more likely to get to their destination even during times of crisis. The 3PL partnership can prove especially useful if you have a B2C/B2B digital commerce arm that directly gets your product to buyers.
Simulation and scenario planning
Supply chains are inherently complex, and it is difficult to fully envisage the numerous scenarios that the hundreds of moving parts could unearth. Still, simulation and scenario planning can help you anticipate potential problems before they become a reality.
For instance, the digital twin technique allows manufacturers to proactively tackle volatility and crises by simulating supply chain performance weeks in advance. Insights in this technique can pinpoint the suppliers and customers who are more likely to be impacted by a disruption. That way, your company can deploy appropriate communications and mitigation actions.
Conclusion
COVID-19 starkly demonstrated manufacturers could not afford to focus on supply chain efficiency at the expense of supply chain resilience. The businesses that thrive long-term build agility into their supply networks, thus embedding adaptability to unexpected large-scale disruption. By applying these seven strategies, companies can strengthen their supply chains over the long haul and ensure business continuity.
In the short term, supply chain resilience is costly and will hurt the bottom line. Longer term, though, it offers a more attractive value proposition.
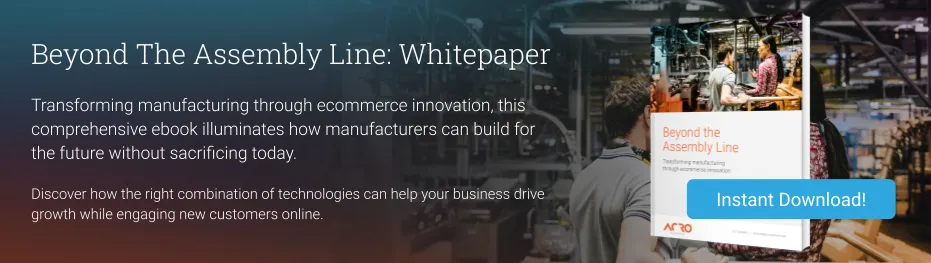
About the author
Jake Rheude is the Vice President of Marketing for Red Stag Fulfillment, an ecommerce fulfillment warehouse born out of ecommerce. He has years of experience in ecommerce and business development. Jake enjoys reading about business and sharing his experience with others in his free time.